Tata Steel’s Spares & Services Department organizes Joint Mass Communication Program (JMCP) at Fabrication Shop of Spares Manufacturing
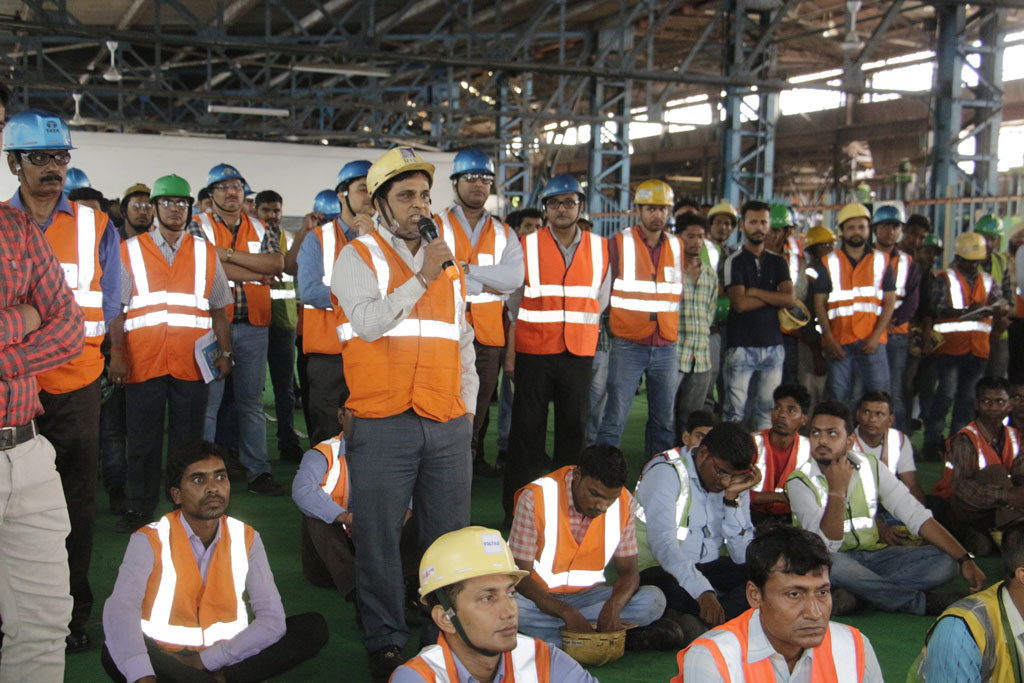
Tata Steel’s Spares & Services Department today organized a Joint Mass Communication Program (JMCP), which is a communication forum where the senior leadership interacts with the shop floor contractor employees to improve workplace safety and get their involvement in the “Zero Harm to Contractor Employees” program.
Mr Avneesh Gupta, VP (Shared Services), Tata Steel, graced the occasion as the Chief Guest, while Mr Shahnawaz Alam, Vice President-TWU was the Guest of Honour. Mr Dinkar Ananda, Chief (Spares & Services), Mr. Sanjay Mishra, Head Safety-TSJ and Mr. T. Roy Choudhury, Head Spares Manufacturing were present on the occasion. The gathering included many Departmental Heads and other officers, Union Committee members of TWU, Supervisors, and contractor workers.
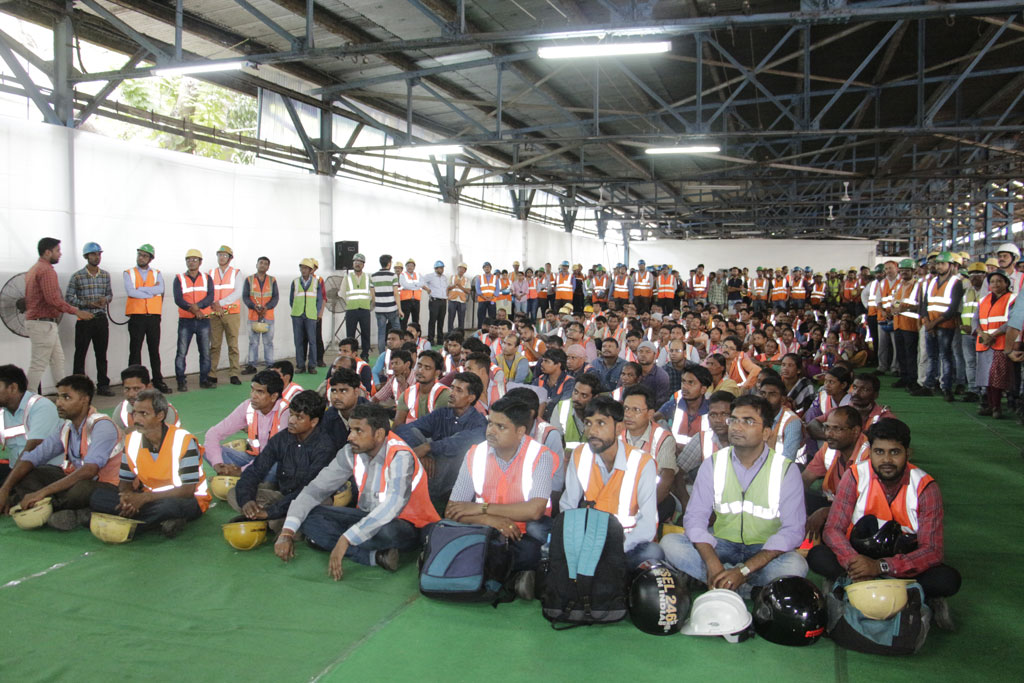
Speaking on the occasion, Mr. Avneesh Gupta said “Nothing is more important than workers safety and well-being. Zero Harm should be our focus, and how you get trained, how you deploy learnings at workplace, how you internalize training and learnings will determine how early we can achieve the Zero Harm goal. I am certain, that together we will achieve this and your part in this safety journey is very important. I am satisfied about the suggestions received and assure you these will be addressed. Please report, escalate any safety concerns, so that appropriate mitigations measures are taken. You may use the hotline service Speak Up for reporting any safety violations while remaining anonymous or having to reveal your identity”.
Mr Shahnawaz Alam explained the safety initiatives taken by the Company for reducing risks at workplace and improving the safety environment. He congratulated all the 4 star rated vendors and encouraged them to keep doing well. According to him, one should “sustain the Safety performance, which would lead to achieving a “Zero Harm” workplace”. He pointed out the success of the Mentor-Mentee program and congratulated the “Zero LTI” performance of the departments. He assured that the amenities would be improved and also informed about the facilities of skill certification and training facilities available for vendors.
Earlier, Mr Dinkar Ananda, welcomed the gathering and set the context of the Program. Mr. Chandra Bhushan Prasad, Safety Officer, highlighted the Departmental Safety performance including Contractor AICs of: (1) Spares Manufacturing, (2) Engineering Services, (3) Equipment Maintenance Services and (4) Infrastructure Planning and Development (IPD), all units of Spares & Services under Shared Services Division of Tata Steel.
Highlights of the Safety Performance of the departments were as under :
Spares Manufacturing | Engineering Services | Equipment Maintenance Services | IPD |
Zero LTI for the last 4 years | Zero LTI and zero first aid in FY’19 | Zero LTI in Fy’19 | Zero LTI & First aid |
Zero first aid case for the last 3 years | |||
Mentor-Mentee programme started for covering 100% contract workforce | Mentor-Mentee programme started | Zero Harm campaign | Implemented various projects, facilities and amenities |
30% reduction in road Asafety violation | 50% reduction in road safety violation | Good reduction in road safety violation | Zero road safety violation |
Mr. Mishra, Head Safety-TSJ, spoke about safety incidents and learning incorporated therein. “Safety emanates from being aware and alert. All the incidents happened due to violation of established procedures and in not following basic safety norms and Emergency precautions at the workplace”, he said.
During the Open sessions, safety related concerns and suggestions on amenities were discussed and appropriate actions and ways of implementation and improvement were agreed to.
Mr. T. Roy Choudhury, proposed a vote of thanks, reinforcing the importance of safety in day to day work.
About Tata Steel
Tata Steel Group is among the top global steel companies with an annual crude steel capacity of 33 million tonnes per annum (MTPA). It is one of the world's most geographically-diversified steel producers, with operations and commercial presence across the world. The group (excluding SEA operations) recorded a consolidated turnover of US $22.67 billion in the financial year ending March 31, 2019. In 2018, Tata Steel acquired Bhushan Steel Ltd (now renamed as Tata Steel BSL Ltd).
A Great Place to Work-CertifiedTM organisation, Tata Steel Ltd., together with its subsidiaries, associates and joint ventures, is spread across five continents with an employee base of over 65,000.
Tata Steel retained the Industry Leader position in FY18 and ranked second overall in the DJSI assessment, 2017. The Company has been recognised as the Climate Disclosure Leader in ‘Steel category’ by CDP (2017). Besides being a member of the World Steel Climate Action Programme, Tata Steel has won several awards including the Prime Minister’s Trophy for the best performing integrated steel plant for 2016-17, ‘Corporate Strategy Award’ by Mint (2018), Golden Peacock Award for Risk Management (2018) and Best Risk Management Framework & Systems Award (2019) by CNBC TV18. The Company also received the ‘Most Ethical Company’ award from Ethisphere Institute for the eight time (2019), Steel Sustainability Champion (2018) by the World Steel Association, Dun & Bradstreet Corporate Awards (2018), Golden Peacock HR Excellence Award by Institute of Directors (2018), ‘Best Companies To Work For’ recognition by Business Today, 'Asia's Best Integrated Report' award by the Asia Sustainability Reporting Awards (2017), among several others.
In 2018, the Company launched a corporate brand campaign #WeAlsoMakeTomorrow. www.wealsomaketomorrow.com
For corporate information, visit www.tatasteel.com and follow us on
Disclaimer
Statements in this press release describing the Company’s performance may be “forward looking statements” within the meaning of applicable securities laws and regulations. Actual results may differ materially from those directly or indirectly expressed, inferred or implied. Important factors that could make a difference to the Company’s operations include, among others, economic conditions affecting demand/ supply and price conditions in the domestic and overseas markets in which the Company operates, changes in or due to the environment, Government regulations, laws, statutes, judicial pronouncements and/ or other incidental factors.