|
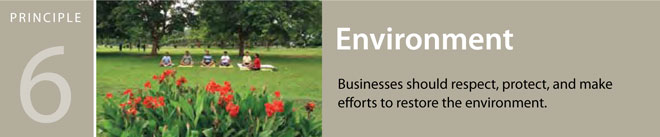 |
Tata Steel has always adopted a proactive approach to the conservation of the environment. The Company's actions are guided by the Tata Code of Conduct, Tata Climate Change Policy, Tata Steel's Vision and Environmental policy.
|
Resource conservation
Integrated steelmaking requires large amounts of raw materials such as iron ore and coal. To ensure optimal use of resources, the Company's policy of reduce, reuse and recycle has been embedded in its processes. Efforts to improve performances have resulted in considerable reduction in the use of energy and natural resources.
The main raw material used across all three locations in Tata Steel Thailand is ferrous scrap, which is fully recyclable. At NatSteel, scrap metal generated within the plant is mostly recycled internally. In 2011-12, the percentage of recycled input materials accounted for 2.36% of the total billet production at NatSteel.
|
Research and development of innovative technologies and processes for Ore and Coal Beneficiation
Raw material cost is critical to the sustainability of steel manufacturers. Raw materials used for steel making are not renewable. Therefore, R&D and operations seek to enhance yield and maximise utilisation of raw material. Innovative application of Jigs to beneficiate iron ore to control Alumina, processes to reduce slime generation, research to produce clean coal at optimal yield and plant rejects to produce concentrates are targeted to achieve this objective.
|
Process optimisation, waste management through reduce, reuse and recycle
Advanced techniques are used to extract iron and carbon, by reusing most of the residual materials through sinter plants, steelmaking and coke ovens, replacing primary raw materials and reducing overall CO2 emissions.
The most significant by-product of steel making, in terms of quantity, is blast furnace slag. It is used as a substitute for clinker in the cement industry. Steelmaking slag is used for civil engineering
purposes and agricultural applications by TSE. Tar and benzole derived from the coke-making processes are used by chemicals industry.
EAF slag, a byproduct of NatSteel's operations, is further processed by a third party for use as road
surfacing material. In Financial Year 2011-12, EAF slag accounted for approximately 14.53% of the crude steel produced.
Relatively large volumes of water are used by all steel manufacturing units, mostly for non-contact cooling and is primarily reused. Tata Steel India reported an 18% decrease in specific water consumption over a ten year span from 7.1 m3/tcs in Financial Year 2002-03 to 5.8 m3/tcs in Financial Year 2011-12.
In Europe, the Company is developing a tool that will provide a more accurate measure of fresh water
consumed per tonne of steel produced to target additional water efficiency schemes.
All industrial cooling water processes at NatSteel use NEWater, a high-grade reclaimed water produced from treated, used water that is purified further using advanced membrane technologies. At NatSteel, 100% of the water is recycled and reused a few times before eventual discharge into the public sewage system.
|
Adoption of green and clean technologies, best operating practices and process upgradation
Appropriate measures for environment protection are taken by adopting BAT (Best Available Technology) and designing pollution control infrastructure to achieve discharge and emissions within statutory limits.
An Environment Impact Assessment is undertaken prior to the implementation of capital projects and appropriate environment management programmes are implemented with the project.
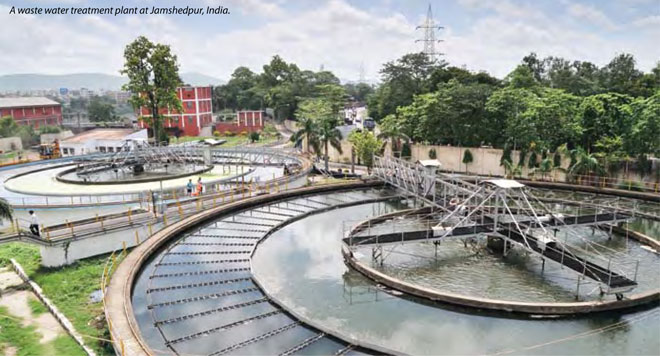
A waste water treatment plant at Jamshedpur, India.
Tata Steel adopts best practices to prevent, or otherwise minimise, mitigate and remediate, harmful effects of mining operations.
Some of the environment friendly technologies adopted in Financial Year 2011-12 include installation
of a tailing de-watering plant for the first time in India to nullify the requirement of a tailing pond and the use of a pipe conveyor to reduce dust generation at the Jamshedpur Works.
|
Mitigating the impact of Climate Change
Although emissions are an area of critical concern for steel manufacturers, Tata Steel believes its
products are part of the solution to climate change, as steel has inherent environmental advantages,
such as being durable, adaptable, reusable and recyclable.
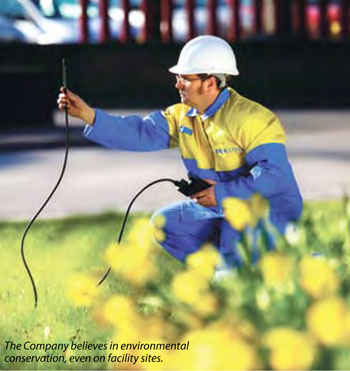
The Company believes in environmental conservation, even on facility sites.
Tata Steel revised its emission performance target during 2009-10 to be consistent with the World Steel Association (worldsteel) scope for reporting. The current targets, which are provisional and are under review, pending regulatory developments, in both Europe (EU ETS Phase III) and India (Perform, Achieve and Trade), are to reduce emissions on a Group-wide basis.
Tata Steel's Jamshedpur Steel Works achieved the best ever direct CO2 emission intensity (under scope-1 of worldsteel methodology) in Financial Year 2011-12 with a rate of 2.27 tCO2/tcs, that is 1.6% lower than 2.31 tCO2/tcs achieved during Financial Year 2010-11.
The total CO2 emission (scope-1, 2 and 3) for Jamshedpur Steel Works during Financial Year 2011-12 at 2.499 tCO2/tcs surpassed the lowest ever achieved rate of 2.504 tCO2/tcs (Financial Year 2009-10) and 2.513 tCO2/tcs (Financial Year 2010-11) .
In India, the Company has developed a Roadmap for reducing CO2 emissions intensity to retain its position as the Indian benchmark in steel-making through the 'Blast Furnace route1.
CO2 emission within European operations during Financial Year 2011-12 were 2.0 tCO2/tcs. The overall Group emissions were 2.1 tCO2/tcs. Compliance with environmental permit conditions continued to be high across TSE. In Europe, the Company is working with other steelmakers on a longer term research and development project, ULCOS (ultra low CO2 steelmaking), to develop breakthrough technologies which can reduce CO2 emissions per tonne of steel produced by at least 50%.
NatSteel had set a target of reducing its CO2 intensity to 0.476 tCO2/tcs by 2012. In Financial Year 2011-12, CO2 intensity for NatSteel was 0.459 tCO2/tcs. The energy intensity of steelmaking at NatSteel Holdings was the lowest ever at 1.613 GCal/tcs and the total energy consumed for steelmaking was 1,233,233 GCal.
|
Environment Management Systems (EMS)
All of Tata Steel's manufacturing sites and raw material locations in India have implemented environmental management systems certified to ISO 14001. The Raw Material Division has a formal Quality, Environment and Occupational Health and Safety (QEHSM) management system. Reviews and audits are conducted at fixed intervals to achieve continual improvement. In case of a breach in environmental norms, the incident is
investigated to establish the root cause and implement corrective actions to ensure it is not repeated.
|
Employee participation
Employees at several sites have established very active energy and environment committees - such as 'Clean, Green and Safe' in Singapore, 'Green Team' in Canada, the 'YmGreen' initiative in the Netherlands and the 'Greenfection' campaign in India. The Company's technical staff and engineers are trained to identify energy-saving opportunities in drive trains (drive controls, motors, couplings and prime movers), which have resulted in significant savings in energy.
In India, an environmental performance report is regularly sent to statutory bodies. This includes monthly reports to State Pollution Control Boards and half yearly reports to the Ministry of Environment and Forests (MoEF) by operating sites in India and quarterly reports by the Raw Materials Division to the Director General, Mine Safety. Real time environment data of the Steel Works is displayed at its main entrance.
Some of the significant issues dealt with by the Indian operations during the year are as below:
- The higher emissions at Sinter Plant No. 3 were reduced by commissioning Best Available Technology - Coromax ESP - in January 2012, in compliance with statutory limits.
- In order to improve LD Slag disposal practices, the Company has initiated actions at Bagunhatu as prescribed by experts.
On the matter of spillage of fuel oil into the river Tees in the north-east England in September 2008, Tata Steel was fined £8,000. While delivering the verdict, the regulating authorities noted Tata Steel's prompt and effective response to the original incident, a high level of cooperation between Tata Steel and the Environment Agency and the Company's good record in the UK.
|
Extending environment management across the supply chain
The environmental impact of the movement of goods and products, though not captured due to a large global vendor base, is mitigated by complying with procedures laid down under the ISO 14001 standards for vendor
registration and contractors. This is being done to reduce air pollution and vehicular emissions at operating sites.
|
 |
SUSTAINABILITY IN ACTION
|
|
– |
The EU Emissions Trading Scheme (EU ETS) is a 'cap and trade' scheme covering all large electricity generators and industrial emitters of greenhouse gases (mainly CO2) within EU Members States. This sets a ceiling on the total amount of greenhouse gases (GHGs) that can be emitted in a multi-year phase. |
– |
In 2013, the ETS will move into its third phase (2013-2020) and the supply of emissions allowances will be further tightened and set on a trajectory to -21% by 2020 compared to 1990 emission levels. Electricity generators will have to pay for all their allowances through an auctioning
process but because the steel industry is classified as being at risk of 'carbon leakage', the sector should continue to receive a free allocation, although it will now be based on a CO2/tonne benchmark of the top 10% best performing sites multiplied by the average output in recent years. |
– |
The above proposals are being discussed with various stakeholders. Tata Steel continues to make efforts to look for solutions that will help reduce its carbon footprint in the future.
|
|
|
|
|