|
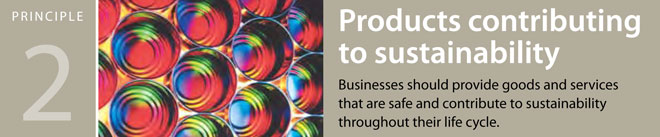 |
Tata Steel has always adopted a holistic approach to product development and resource utilisation. Comprehensive analyses of the environmental impacts associated with the safety of products, processes and resource utilisation are obtained through Life Cycle Assessments (LCA), aiding the Company to inform its customers and stakeholders about product properties, safe usage and proper disposal, as well as the environmental impact of products taking into account that steel is 100% recyclable.
Opportunities for improvements in environmental and sustainability performance are identified through a robust Total Quality Management programme, which spans the entire value chain. During 2011-12, the key activity of the European Sustainability Management Group, comprising senior representatives across functions, was to link stakeholder expectations with the Company's processes and performance on key sustainability-related issues. A new business vertical within the Indian operations is engaged in driving sustainability across all units.
|
Product safety and optimal utilisation of resources over the life cycle of the product
To support dialogue within the value chain and drive continuous improvements in the sustainability
performance of its steel and steel products, European operations have developed a sustainability assessment
tool to specifically investigate sustainability throughout the life cycle of the product, including manufacturing, processing, use-phase and end-of-life. This industryleading sustainability assessment model, which is now being applied to all new product developments, is helping Tata Steel deliver tangible sustainability benefits throughout the value chain.
The LCA projects undertaken in the last decade have greatly improved the environment performance of
the Company. An LCA project initiated in 2011-12 by the Indian operations is aimed at developing an Environmental Product Declaration (EPD) for Tata Steel's rebars, to provide relevant environmental information
along the product's value chain.
Outcomes from the Gate-to-Gate analysis conducted for the coke plant at Jamshedpur in 2010-11 is expected to reduce the overall emissions from the coke plant by 20%. LCA projects on coal mining and washing, conducted at West Bokaro and Jharia in 2003 and 2006, led to the recycling of rejects, greater conservation of natural resources and a drop in emissions of various polluting gases. The LCA study for cold roll sheets conducted in 2004 prompted improvements in gas recovery from the coke plants, a virtual switch from coal to gas as the energy source for power generation, and consequently a drop in CO2 gas emission, besides more than 90% utilisation of Blast Furnace slag.
|
 |
The Company's range of advanced high strength steel makes cars lighter and more fuel-efficient. |
In Singapore, NatSteel uses only recyclable ferrous metal waste for processing into high quality construction steel, through one of the most energy efficient processes globally.
Energy-efficient technologies employed in NatSteel's Singapore plant include the use of the shaft electric arc furnace for waste heat recovery as well as billet hot charging into the reheating furnace. These have made the plant and rolling mill one of the most energy-efficient in the world.
|
Educating consumers of their rights, product properties, safe usage and disposal of products
A Retail Identity Programme in India, including development of dedicated channels, Company-certified retailers and branded outlets for its rebars (Tata TISCON) and steel roofing solution (Tata Shaktee), has transformed steel retailing in the country. The programme has created a vast network of dedicated distributors, exclusive showrooms and dealers covering all states and districts of the country. These distributors facilitate extensive dissemination of knowledge to consumers. Comprehensive product information, knowledge of applications and consistent pricing across shops enables consumers to fit a product to their budget.
Rural marketing programmes reach out to nearly 3.5 million potential customers every year. In 2011-12, there were more than 6,000 such programmes. The retail reach of Tata TISCON was enhanced by 27% during the year, increasing its dealer network from 2,750 to 3,500. Cross-functional product teams interface with a diverse range of end users including OEMs, architects, homeowners, masons, etc. through programmes such as Learning, Interaction, Networking, Knowledge Sharing (LINKS), Responsible Architectural Initiatives and Structural Engineering (RAISE), Build Wise, initiatives for influencer management, knowledge-sharing initiatives for the Cold Rolled and Galvanised Plain customers, along with the Customer Engagement Programmes - Value-in-Use and Wired2Win.
|
 |
SUSTAINABILITY IN ACTION
|
|
– |
European Sustainability Management Group comprising senior representatives from Environment, Marketing, Corporate Communications, Procurement and Hub teams, makes the link between stakeholder expectations and the Company's performance on sustainability. |
– |
Business vertical of sustainability created for Indian operations. |
– |
Sustainability Assessment Tool used in European operations. |
– |
Environmental Product Declaration (EPD) project as part of the Indian operations. |
– |
6,000 Rural Marketing Programmes, reaching out to nearly 3.5 million potential customers. |
– |
Rise in Tata TISCON dealer network from 2,750 to 3,500. |
– |
Embossing of brand logo on all Tata Steel products. |
– |
Technology Roadmap with a dual mission - to ensure resource-efficient product designs and deploy eco-friendly technology. |
|
|
Making manufacturing processes and technologies resource efficient and sustainable
Tata Steel's Technology Roadmap, released in 2011-12, is aimed at ensuring that product designs are resourceefficient and deploy eco-friendly technology. A result of a consultative process, the Roadmap provides a long-term view on aspects, such as emerging market trends, product applications and emerging technologies, besides identifying gaps and opportunities based on present and future needs, and showing the way forward for technology advancement by pursuing both innovative improvements and path-breaking technologies.
The Roadmap also integrates and aligns projects undertaken by the R&D and Technology Groups with Divisional and Corporate goals so as to realise the Corporate Vision of sustainable growth. Tata Steel's R&D efforts focus on breakthrough technologies (through its participation in the ULCOS project) and Raw Material Beneficiation to effect reductions in greenhouse gas emissions. The Company is measuring and monitoring CO2 emissions from all its major production facilities across the globe to reduce CO2 emission intensity by continuously improving internal operations, effecting process improvements and optimising raw material usage.
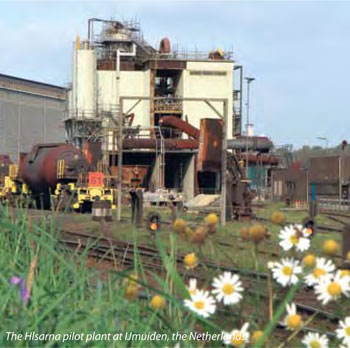
The HIsarna pilot plant at IJmuiden, the Netherlands.
|
New technology development, deployment and commercialisation
Tata Steel fosters a culture of innovation and continuous improvement, which helps it to continuously review its product mix, develop first time products and services and commercialise them, for example, hydroforming of fuel tanks, rebars which effect savings in steel consumption by weight and Galvano, an eco-friendly steel produced through lead-free coating chemistry.
Life Cycle Assessments are extensively used to advise customers at the design stage on the sustainability of downstream products made from steel. Development of steel grades and steel products that improve the sustainability performance of customers is regarded as work-in-progress at Tata Steel. These approaches have led to energy-efficient products within end-user markets. For example, the Company's range of advanced, high-strength steels make cars lighter and more fuel efficient, while its specialist construction products play an integral part in delivering energy-efficient buildings and reductions in steel consumption by weight.
Tata Steel has, in partnership with Dyesol, developed the world's largest dye-sensitised photovoltaic module, a big step in the development of micro-energy generation within buildings. The partnership successfully produced hundreds of metres of printed steel and polymer film, establishing the feasibility of a continuously printed dyesensitised product.
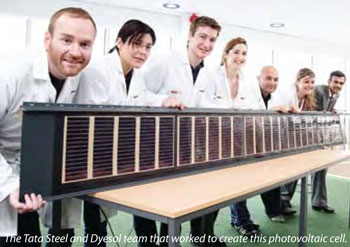
The Tata Steel and Dyesol team that worked to create this photovoltaic cell.
Adoption of technologies such as Thin Slab Caster and Rolling Mill as well as the Continuous Annealing and Processing Line are leading to products with energy efficient end applications.
|
Recognising and respecting the rights of owners of traditional knowledge and intellectual property
Tata Steel's locational proximity to indigenous communities makes it conscious and sensitive to the
need to preserve their unique culture and traditional knowledge. Through its Tribal Cultural Society, the Company runs centres for teaching and preserving the Ho and Santhali scripts to keep them alive, an imperative for the perpetuation of traditional knowledge.
In recognising and preserving intellectual assets, Tata Steel addresses two principle challenges. The first challenge is the commercialisation of its patents to unlock the value of its IP portfolio. This process is benchmarked against international best practices. Seven companies worldwide have shown interest in the first patent placed in the market by Tata Steel for on-line property prediction in the hot strip mill. Twelve copyrights for e-learning packages have been identified for commercialisation as pilot cases, with 78 companies eliciting interest in them.
The second challenge is to retain a claim on its IP while sharing developmental knowledge with international partners. It requires a fine balance between understanding of technology and legal negotiation skills. Tata Steel is reviewing international best practices to arrive at this balance.
|
Reduce, reuse and recycle to optimise resources utilisation
Raw material, energy and water requirements are continuously tracked and compared with global industry standards or benchmarks to optimise resource efficiency based on the twin drivers of resource conservation and cost reduction. For example, the Company continuously strives to reduce the carbon rate in its smelting operations through the adoption of efficient processes, raw material beneficiation and initiatives to recover iron from wastes such as slime, along with in-house improvement through process control.
Wastewater recovery systems increasingly recycle treated effluents back to the steel manufacturing process thereby minimising water uptake. The Jamshedpur Steel Works sources 14.5% of the 29.2 MGD of water consumed by it from recycled effluents. Tata Steel's ore binding programme at its ore mines recovers clean water from the slime pond.
All products made by Tata Steel are fully recyclable. Hence the Company looks upon steel scrap as a recycled raw material resource integral to its steel-making processes. All steel-making units use a proportion of recycled steel as an input material, though the specific proportion of recycled content varies and is optimised within each of its steelmaking operations.
|
|
|