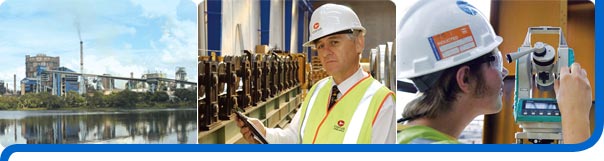
Continuous Improvement
From the year 2002, the global steel industry grew with the steel demand shooting from 2% to 8% year on year. The Indian steel industry with its 43 million tonnes of steel production in a booming economy, was also showing rapid growth. At such a time when the situation could not have been any better, in 2008 the global economic slowdown cast its shadow on almost all industries including steel. The steel industry was suddenly faced with a high locked up capital and is now having to resort to serious firefighting measures to overcome the current scenario.
Tata Steel India was also impacted by the economic slowdown. However, it still had the confidence that it would be able to continue to perform much better than many others in the industry. This confidence is an outcome of its understanding the cause and effect and its ability to use Total Quality Management (TQM) to achieve its desired goals. While there is no quick fix approach on this journey, Tata Steel believes that long years of perseverance and belief are needed to continue the journey of excellence.
Tata Steel has been pursuing TQM for business excellence formally since the late 1980s. With the vision of becoming a world-class steel company, it adopted various popular improvement initiatives practiced around the world. All this has resulted in recognition by various agencies from accreditation on ISO standards for quality systems, business excellence awards based on Malcolm Baldridge model- JRDQV award, EFQM (European Foundation for Quality Management) model- CII Exim Bank award and JIPM (Japanese Institute of Plant Maintenance) – TPM Excellence award to name a few.
With these laurels, Tata Steel believed that it was on the right track to be deemed a TQM company.The process of working for and winning the coveted Deming Application Prize in 2008 has also been a humbling and enlightening experience for Tata Steel. Humbling, because it helped Tata Steel pinpoint inconsistencies in its approach of managing its business based on logical principles that are often camouflaged during the good times and surface only during a crisis. Enlightening, because the same process has helped Tata Steel focus on its strengths in areas that are most critical to its business.
The road to the Deming Application Prize forced Tata Steel to research some of the basic systems which exist (but may not be apparent) in an integrated steel industry.
Understanding Customer Needs
Integrated steel plants are capital intensive with a long payback period. It is natural therefore, for steel plants to maximise capital productivity through volumes. Like any other steel plant in the past, Tata Steel’s focus had been internal, primarily on cost and volumes. With its growing understanding of TQM and Theory of Constraints (TOC) on the journey towards the Deming Application Prize, its customer focus and approach to the market has undergone a significant change. It started changing the levers of improvement from an internally focussed efficiency driven culture to a culture of value creation with customers and suppliers.
Some specific approaches in the market that Tata Steel started were Customer Value Management (CVM), Retail Value Management (RVM) and Solution for Sales (SFS). These approaches focussed on the “needs” rather than “wants” of the customer. It is important to note that these approaches were continued or initiated in a supplier’s market condition when the steel cycle was on a high. Even as the overall market experienced seasonality of demand, the retail sales (through which a significant volume of construction bars is sold) of Tata Steel India was rather insulated.
In a downturn, it is often tempting to chase sales. This inevitably results in a price war which is detrimental to the organisation and the industry. The objective therefore should be to create value for the customer or in other words, should help the customer make money. The assumption that the customer makes money when prices are low can often be unfounded. The journey towards the Deming Application Prize using TQM, provided a deep insight of the needs of the customer and how to capitalise on the need without jeopardising mutual interests.
Mirroring the CVM process, Tata Steel initiated the Supplier Value Management (SVM) programme with its key suppliers, which also works on the ‘one firm concept’ with the objective of mutual value creation. Similarly, focussed approaches to improve and effectively manage raw materials have been undertaken with the objective to maximise the use of captive resources.
Infrastructure Strengthening
In its zeal to constantly conquer new frontiers especially during a boom period, maintenance, sustenance or standardisation of the current practices are often ignored by an organisation. In good times, the weaknesses in the daily work management system are not focussed upon which later are exposed even during mild storms in the market or economy. Robust daily work management practices, a clean and safe work environment and consistency and stability of processes are essential building blocks to weather the economic storm. A robust base is essential to improve and sustain gains. The road to the Deming Application Prize emphasised the importance of a robust base and the process of ensuring deployment of the same.
The Improvement Philosophy
Just sustaining the current performance is inadequate under any environment. Today, most organisations continuously strive to improve. However, the following three aspects often remain as weaknesses:
- Improvement is often inward looking and relatively less effort is made in distinctly differentiating the offerings to the customers
- The objectives may not be challenging (aspirational)
- The means to bring about improvements are often not tested for causality i.e. the means are not checked for necessary and sufficiency conditions to meet the desired objective. Failure to test interventions against appropriate causality leads to making the ‘One size fits all’ approach to target setting as well as the choice of tools and techniques.
The company’s ASPIRE technique helps to set goals and choose the appropriate tools. Under this, certain parts of the planned improvements are checked for causality, explored for means (causes) and then the implementations are carried out using differentiated tools and techniques. For the remaining parts of the aspirational goals the means are innovated as we proceed in the implementation journey.
The future belongs to organisations that can increase the pace of standardisation (to have a robust base), improve quickly on their current operations and continuously innovate to differentiate themselves from the rest.
This can only be achieved by leadership, passion, process and knowledge.
Tata Steel’s TQM journey has made it acknowledge the fact that the only sure way to prosperity in the long run, is to ensure value creation for the system as a whole, starting from the customers to the suppliers.
Performance Improvement in the Tata Steel Group
Following its principle of driving all processes towards quality under TQM, Tata Steel in January 2008 set up the Performance Improvement Committee (PIC) to drive performance improvement on a continual and accelerated basis. In the next few months, the framework and structure of the PIC was finalised, with Performance Improvement (PI) Groups for iron making, steel making, flat rolling, long rolling, maintenance, distribution service centres and building systems. RD&T also represented in most of the PI teams under each of the groups.
Initially, projects were identified with bottom-line impact of $180 mn, of which 30% were cost projects and the balance were throughput (volume) related. With the change in market situation in H2, the sites reworked their projects and now cost related projects comprise 40%, though the total benefits have reduced to $ 150 mn.
Early Success Areas
Some areas where Tata Steel’s effort at continuous improvement bore fruit include:
- Higher usage of processed reverts at Scunthorpe and Port Talbot
- Reduction in hot metal manganese at Port Talbot
- Bottom stirring at IJmuiden leading to improved converter life and yield
- Higher usage of Low Cost Carbon Source (LCCS) in the blend at IJmuiden, Port Talbot and Scunthorpe
- Vessel life improvement at Jamshedpur and Scunthorpe
- Blast Furnace and Coke Ovens operating process for lower production levels developed and successfully implemented in Tata Steel European operations without compromising equipment health and safety
Coke Self Sufficiency
Coke oven availability improvements
- Improvement in caster speed at LD2, Jamshedpur by implementing shop tracking system
- Improvement in HSM productivity, Jamshedpur by mill pacing model and effective shutdown management
- Improvement in PLTCM productivity at CRM, Jamshedpur by looper optimisation
Change In Performance Culture
The Performance Improvement journey has resulted in some positive changes in the performance culture:
KPI Comparisons
Each PI team has identified its top three to seven KPIs which are being tracked and compared across sites each month – commencing from July 2008. Such KPI comparisons have led to discussions on areas where there have been significant performance gaps within the Group and often, these have resulted in improvement project opportunities.
Bottom line Orientation
Most projects are being identified with a view towards impacting bottom line improvement and most of the projects are conceptualised along with an expected financial benefit.
Knowledge Exchange with a Purpose
Within the PI teams, knowledge exchange is principally to address common operational issues, address common weaknesses and pain areas and significant KPI gaps. For example, Blast Furnace PIT and Coke PIT have discussed how to manage operations at lower production levels in a safe manner and without damaging the equipment.
As part of the agenda, the PIC meetings drive specific knowledge exchange opportunities.
People Involvement
The PI Team (PIT) meetings and the resulting project opportunities have had a positive influence on involving more people at each site in taking on improvement projects and participating in PIC / PIT reviews.
With a legacy of over 100 years, Tata Steel already had practices in place to manage its operations and situations. In the last twenty years, it has explored and practiced a number of improvement initiatives with TQM forming the holistic approach to manage its processes by quality.
Tata Steel believes that this approach will ensure sustainability while continuously improving its current practices to keep pace with changing market requirements.
It constantly strives to break away from the common place and to set new industry benchmarks for others to emulate.