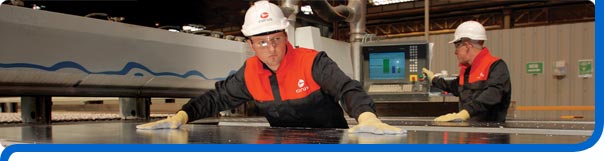
Responding to the Crisis
Some Initiatives by Tata Steel Europe (Corus Group)
Initiatives over the years...
In the past Corus has had to address situations where the market has changed in such a way that simple adaptation has not been sufficient. After evaluating a longer-term view of the market, Corus has restructured or consolidated its manufacturing capacity, invested in the remaining sites to enrich the order book and to enhance capacity in order to meet future demand. Finally and most importantly, the company has continually invested in developing the skills of its workforce.
Between 2000 and 2005 Corus was required to manage fluctuation in European demand and adapt its sites to the changes in the market.
In 2003 Corus began its UK Restructuring Programme. The aim of this was to improve the efficiency of the UK steel making businesses in order to reduce costs and generate cash throughout the economic cycle. Crude steel production in the UK was to be focussed on just three sites – Rotherham, Port Talbot and Scunthorpe – with capacities more closely aligned to likely future demand. The programme required significant investment in the company’s engineering steels business as it concentrated its steel making, casting and rolling at Rotherham. Its aim was to enable Corus Engineering Steels to achieve a competitive position in the European market.
Other investment-led initiatives enhanced and increased the steel making capacity for strip products at Port Talbot and long products at Scunthorpe. These also included an improved process route for wire rod production and adaptation of the medium sections mill to make very long rail, as the existing facilities could no longer meet the needs of the market. Steel making at Llanwern was closed and Teesside Works was no longer seen as core to the company’s needs. However, Teesside would need to be retained until the other investment programmes were completed. This led to the decision to enter into a long-term sales agreement for slabs produced at Teesside.
To complement these changes in its manufacturing capability, Corus embarked on ‘Restoring Success’ – a change programme expected to last three years. A large part of this programme was focussed on skills improvement, examples of which are ‘The Journey’ and ‘World-Class IJmuiden’.
By 2005 Corus had returned to profit. The ‘Corus Way’ programme was launched, which was designed to embed continuous improvement into the culture of the company based on four principles:
- Best Supplier to Best Customers
- World-class Processes
- Selective Growth
- Passionate People